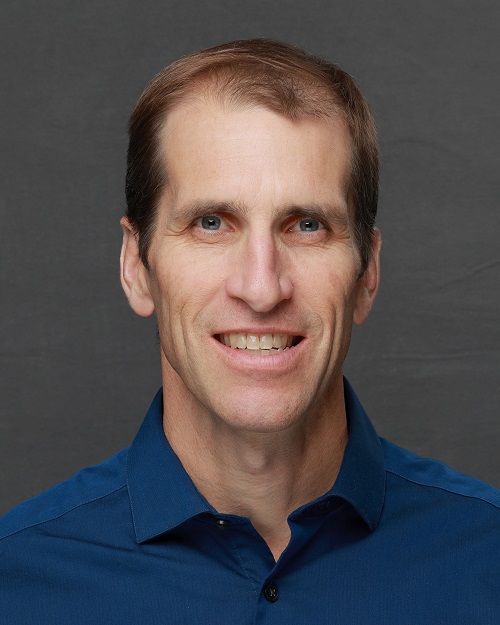
Energy Resources Update
Regional energy sector news continues to be a drumbeat of uncertainty, between oscillating trade policy and staffing changes at the federal level, many questions remain.
Through this season, our utility continues to prioritize power quality and reliability, both supply and delivery, and rate stability.
In October, we transition from a BPA Slice/Block contract to Load Following, a change that provides added stability in both power price and procurement. And as we acknowledge the interdependence across our regional energy system, this utility continues to work closely and collaboratively with both public and private utility partners, and our state and federal elected representatives, to identify and address resource adequacy and transmission challenges.
At the end of this month we invite those of you interested in issues related to planning, policy and economic development to join us for a Community Leader session where we’ll share more about the utility’s current priorities and plans as we work toward state carbon reduction requirements. The event is scheduled for Tuesday, March 25th from 1:00 pm to 5:00 pm and will take place at Clark Public Utilities Electric Center at 1200 Fort Vancouver Way. For those interested in attending, please RSVP to [email protected]
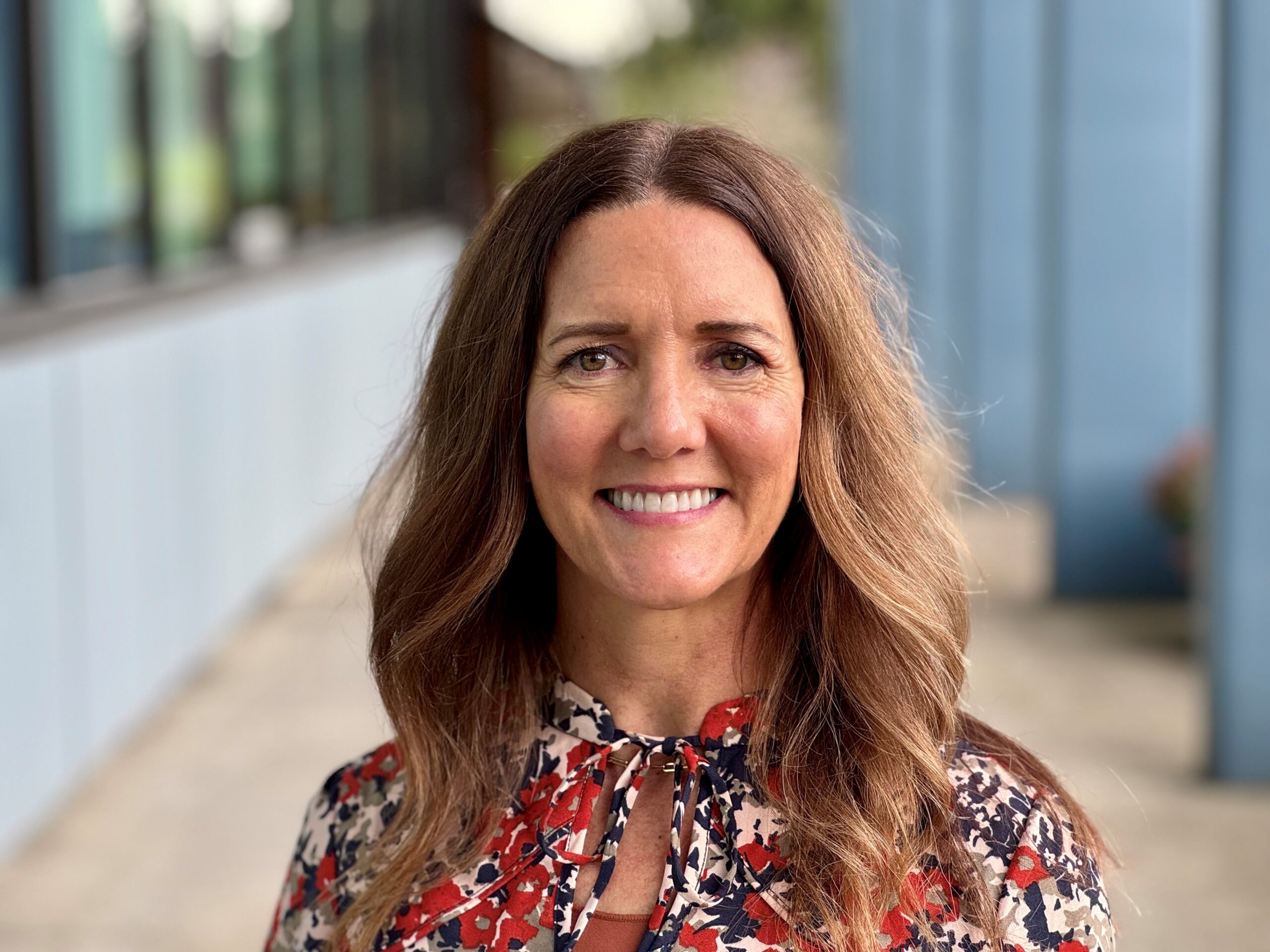
Meet Our New District 1 Commissioner, Sherry Erickson
Commissioner Sherry Erickson was elected to the utility’s Board of Commissioners filling the seat representing areas in north Clark County, previously held by Jim Malinowski.
Erickson has a Master of Business Administration degree from Washington State University and a bachelor’s degree in Mechanical Engineering from Brigham Young University. As a licensed engineer, she worked as a consultant in design, construction, and business management for a variety of clients, including utilities and municipalities.
Erickson is a longtime Clark Public Utilities StreamTeam volunteer, serving on the utility’s Stream Steward volunteer team. Erickson serves on the executive committee of the Columbia River Economic Development Council and as our representative at Columbia Springs, an environmental education center.
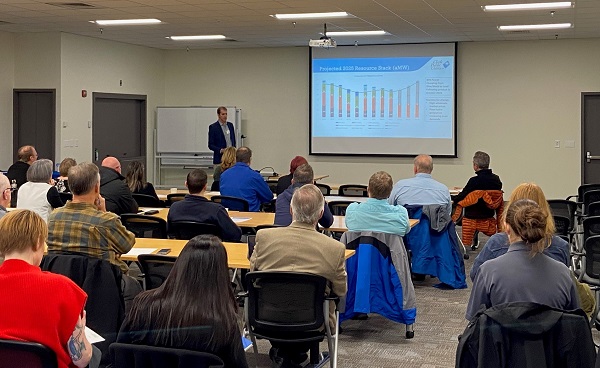
Key Accounts Forum Visits The VIC
The Key Accounts team hosted many of the electric utility’s largest customers during their 14th annual Key Accounts Forum on Thursday, November 21, 2024 at The Vancouver Innovation Center (The VIC).
Representatives from several industries including school districts, municipalities, hospitals, semiconductor manufacturing, ports, and others, were in attendance.
The event kicked off with Steve Andersen, Director of Energy Resources, providing a power supply update as well as plans to reduce our reliance on carbon-emitting resources and incorporate more renewables in order to ensure compliance with the state’s renewable energy standards into the future. He also informed the group of our plans to switch from a Slice/Block product to a load following product from BPA in October 2025.
Clean Energy Program Manager Matt Babbitts gave updates on the WA Clean Fuel Standard, residential EV charging pilot program, and the Industrial demand response pilot.
Key Accounts Energy Solutions Manager Bill Hibbs informed the audience of some new pilot programs that are in the works such as Midstream Lighting, Early Design Assistance, Energy Project Manager, and Retrocomissioning.
Industrial Key Accounts Manager Aaron Frechette discussed the Energy Smart Industrial program, provided additional information on the Industrial Demand Response Pilot, and recapped the industrial savings by sector across the region.
Our concluding speaker was Mark Esrig, Principal at New BluePrint Partners and part of the development team of The Vancouver Innovation Center (The VIC). The future campus will comprise of industrial, retail, and residential mixed-use space along with walking trails and sports courts for a sustainable future. You can learn more about The VIC and its future plans by visiting their website at thevicwa.com.
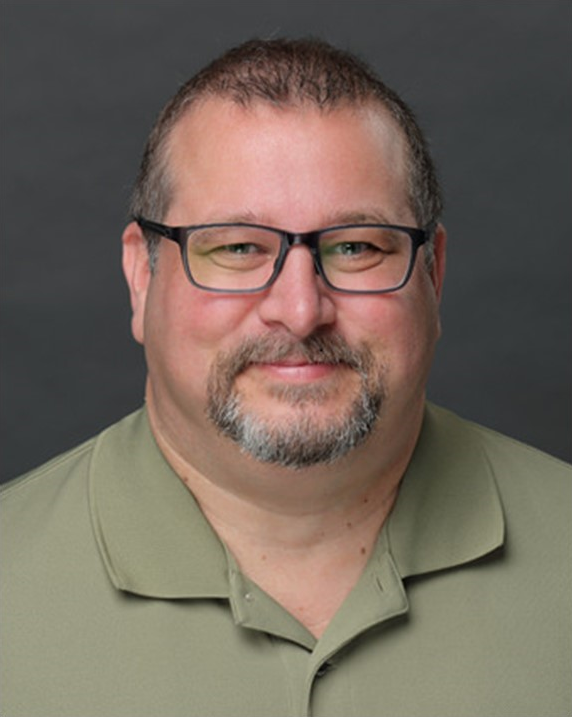
Meet Robert Hill
Robert Hill has transitioned to the Key Accounts team with over 32 years of experience in the utility industry as our Energy Solutions Manager.
Robert spent most of his career leading and working within the Customer Service Department at Clark Public Utilities. In his previous position, he was the Customer Service Manager where, for the past 19 years, he has led the Utility’s award-winning Customer Service Team. Prior to that, he served as the Quality Service Manager.
Robert is a problem solver who cares deeply for our community and our customers. He has consistently demonstrated exceptional care for our residential and business customers, both large and small.
Living in the local area his whole life, Robert finds that working to benefit the local community is one of the most rewarding elements of the job. The Key Accounts Team is thrilled to have Robert join us with his vast experience and broad customer service skills. Don’t be surprised if you hear from Robert in the coming months as he starts supporting our medium-sized business customers.
Welcome Robert!
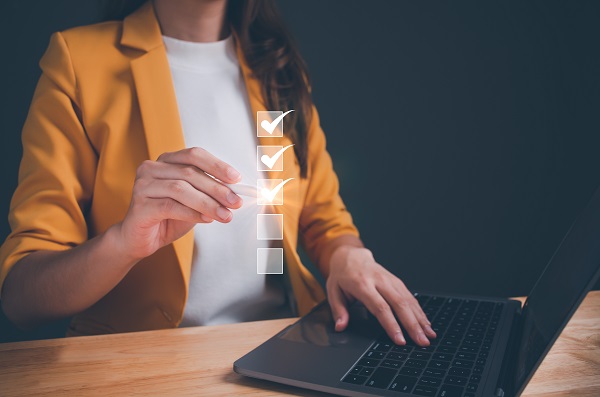
2024 E Source Large Business Customer Satisfaction Study Results
Last year, Clark Public Utilities partnered with E Source to conduct a study of large business customer satisfaction that we use to improve the value of service we deliver to our largest business customers. This nationwide study looks at how our largest accounts interact with their account manager and the Utility, helping our Key Accounts Team see what is important to customers and how we perform compared to those values.
Clark Public Utilities came in second place (just two hundredths off from a first place result) with our score improving from the last study in 2022. Data from the study shows that our large business customers cite providing reliable energy, being trustworthy, and effectively communicating during energy emergencies as the most important attributes for a utility to have.
Data on Key Account Manager attributes most important to our customers include being trustworthy, easy to reach and communicate in a professional and courteous manner. We are proud to say that these utility and Key Account Manager attributes are consistent areas of our focus and attention at Clark Public Utilities.
We would like to extend our thanks to the customers who took the time to participate in the survey. We value the data from this study and are always looking for ways to better serve our customers. If you have any questions on this study, please contact your Key Accounts Manager.

New Program – Midstream Lighting
We are happy to announce the launch of our Business Instant Lighting Discounts (BILD) program. This midstream lighting program offers instant discounts at the point of sale at select distributors in Clark County on select energy efficient lamps at nonresidential sites. These products, including linear TLED lamps and HID replacement lamps, are sold through distributors via a point-of-sale channel, requiring no pre-conditions for participation. The incentives and savings provided depend on the type of lamp, with comparisons made to a baseline determined through regional market analysis. Products purchased through the midstream program are not eligible for incentives through the downstream CLIP program. Capital projects and large quantity lamp installations should be submitted through the downstream CLIP program to maximize incentives for the customer. Below is a list of incentives that are available through this program. Please reach out to Mike Wallace for more information.
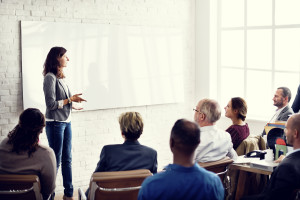
Upcoming Trainings
Clark Public Utilities is a proud sponsor of the 2025 Building Operation Certification program technical webinar series. As a sponsor of the technical webinar series, Clark Public Utilities can offer customers complimentary registrations to the webinars and access to webinar recordings for sessions that have already been offered. The 2025 sessions are as follows:
Artificial Intelligence and the Future of Building Controls & Security – April 16, 2025
Artificial Intelligence (AI) is transforming building automation systems (BAS) and smart buildings by enhancing efficiency, security, and occupant comfort. This webinar will explore some of the potential benefits, challenges, and technical considerations for utilizing AI in BAS.
Retrofitting Fossil Fuel-Based Equipment with Heat Pumps – May 21, 2025
The electrification of fossil fuel-based heating systems will play a significant role in building decarbonization efforts. This webinar will showcase a case study example of a facility that retrofitted their fossil fuel-based equipment with heat pumps and discuss the resulting benefits.
Strategies to Help Reduce Peak Energy Use – September 17, 2025
Reducing a facility’s peak energy use can provide significant savings, especially during peak demand events when electricity prices may be higher. This webinar will explore key strategies to help identify and address peak energy usage, including practical tools, technologies, and real-world examples. Attendees will gain insights into energy management best practices, cost-reduction opportunities, and how to implement effective peak demand solutions tailored to their facility’s unique needs.
Building Walkthrough – Finding Energy Waste – October 15, 2025
This webinar will provide a guide for conducting a building walkthrough, aimed at identifying inefficiencies in building systems and the building envelope. The session will also cover proven strategies and practical solutions to improve overall building performance, reduce energy consumption, and lower operating costs. By incorporating real-world examples, this webinar will equip attendees with actionable knowledge to assess their facilities effectively and implement energy-saving measures.
In addition to sponsoring the webinars, Clark Public Utilities is also offering two $1,000.00 scholarships to individuals working in Clark County interested in completing a Building Operators Certification level I, level II or Fundamentals of Energy Efficient Building Operations course. Please contact your Key Accounts Manager if you are interested in applying for a scholarship.